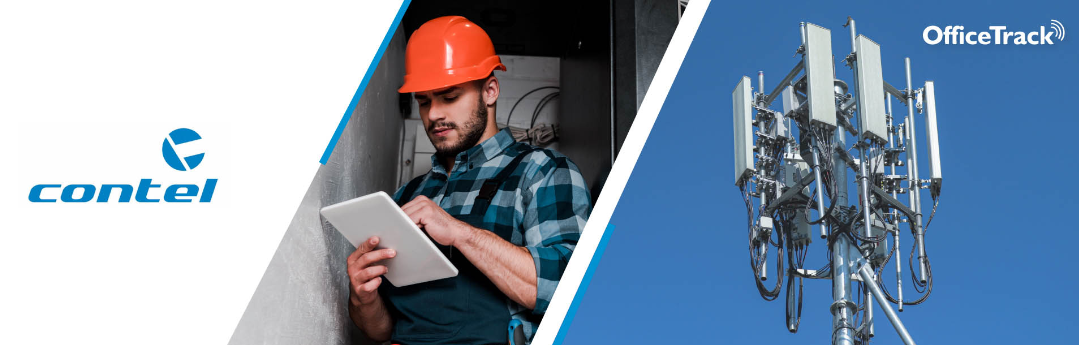
The Field Service App has automated and standardized the procedures for technical visits to telecommunication towers, improving quality and reducing report delivery times.
Brazil has about one hundred thousand antennas and eighty thousand telecom towers installed throughout the country, but with the arrival of 5G they should quadruple, was what was revealed by the Telebrasil 2020 Panel.
According to Luciano Stutz, president of the Brazilian Association of Telecommunications Infrastructure (Abrintel), the sector foresees investments of about five billion reais by the end of 2023. These excellent prospects promise to shake up the entire ICT ecosystem, including tower manufacturing and maintenance.
Contel is a good example of how this market will have to prepare itself to compete and gain larger portions of share.
The company underwent a profound digital transformation, especially in the management of its field resources. This led to an increase in its efficiency and service capability, enabling managers to see its entire external operation without leaving the office.
Challenges in the inspection of five thousand towers
Contel’s O&M (maintenance) area is responsible for the inspection of more than five thousand towers throughout the country. This service includes activities such as: site cleaning, site closure, technical assistance for the metallic structure and equipment installed at the base, among others.
Preventive maintenance is essential, since inclement weather, vandals, birds and animals are always a threat to the proper functioning of telecommunications in the country. Without automation, managing maintenance processes became increasingly challenging.
“Our field technicians inspect towers in the most remote places in Brazil, such as Porto Valter and Marechal Taumaturgo, cities in the state of Acre, which can only be reached by plane. Each visit is crucial for the proper functioning of the network,” said Gustavo Henrique Borges Alencar, Contel’s Chief Operating Officer.
He also commented that the towers receive a technical visit every four months, and that the inspections must generate very complete reports for the clients.
To carry out this mission, the field staff went out with a camera, a cell phone and a pre-printed paper form.
“In the evening, upon arrival at the hotel, the technicians would download the photos and send them along with the report to the company’s offices for the completion of an Excel report.
“This whole process used to take between two and three days, which delayed the arrival of the information to the clients,” he described.
Another problem prior to the digital transformation, was the non-compliance with the checklist required by the client.
“Sometimes, a technician would forget to take a picture in a predefined and mandatory sequence and when he remembered, he was already in another city. So he had to redo the job again. This led to increased costs and more delays,” he said.
Turning the key
Gustavo Alencar says that the technological evolution that the company underwent came about thanks to external demand.
“We knew we needed to automate our processes, but the catalyst was a large customer who told us that their partners would need to adopt an application for reporting. We looked for suppliers and even started to develop an application, but it was that same customer who recommended the use of OfficeTrack, an Israeli field resource management application, which had been chosen as a standard by the company worldwide,” he recalled.
Thus, OfficeTrack, a Field Service application, marketed in Brazil by the consulting firm 3CON, arrived at Contel and began to be used by about fifty field technicians. However, its use went beyond reporting.
The application automated tower inspection processes and the management of external resources, including employee clock-in and clock-out control, accountability and even aspects such as work safety.
It also helped to verify whether technicians were wearing uniforms and personal protective equipment.
The Director recalls that at first there was some resistance from some employees to adopt the new technology, but the ease of use and the advantages of the electronic form proved that the evolution was good for everyone.
“The application reduced problems in visits, cost, timeframes and ensured traceability of each resource in the field. Today we can see our entire operation, we know everything that happens outside the office with precision,” he described.
Alencar highlights the transformations that technical visit reports have undergone, an essential activity: “Our tower maintenance business requires a large number of reports. There are more than 15,000 a year, or about 40 a day. Without automation, this activity used to take a lot of time, a lot of dedicated people and a greater chance of failures and delays. Now, the reports are standardized and practically error-proof, because the application itself avoids failures in inspection and completion. The technician is obliged to obey the sequence established in the electronic form. If you don’t perform a task, such as taking a certain photo, you can’t finish and send the report,” he celebrated.
The new document is filled out from the cell phone, and with a few clicks the technician finishes completing it. In addition to facilitating field work, OfficeTrack is very intuitive when it comes to formatting these forms according to the company’s routines and needs.
“Even without IT knowledge, it is possible to customize the forms so that the application fits our reality and that of each client,” he said.
Return on investment
For the Director, the cost of the application is amortized by avoiding rework.
According to him, errors in the field have been greatly reduced, favoring the optimization of human resources, improving the perception of modernity and efficiency of the processes by customers.
Delivery times have been reduced from days to a few hours. “As we got to know and understand all the advantages of the app, we decided to implement it in most of our customers,” he praised.
When the issue is digital transformation, many companies are not motivated because they fear traumatic processes that may stifle the operation or because of the lack of after-sales support.
Gustavo Alencar attests that Contel has had none of these setbacks.
“The implementation of OfficeTrack in the field or in the back office went smoothly. 3CON provided us with the technical support we needed at every stage, from implementation to day-to-day operations, which made a big difference,” he concluded.